Safe and fair artisanal mining
We help to professionalise artisanal mining operations on site and enable market access, and safe, dignified working conditions at artisanal cobalt mines.
Artisanal mining – an economic development opportunity overlooked
Artisanal cobalt mining is said to provide a livelihood to more than 200.000 men and women. Paying comparatively well and boasting a low barrier of entry, artisanal mining is seen by many as advantageous compared to agricultural or other entrepreneurial endeavours.
This is not a fringe occurrence, but counts for many minerals and gemstones across the global south including tin, tungsten tantalum and gold (3TG),coloured gemstones, diamonds and development minerals – offering a livelihood for more than 40 million people. As such, artisanal and small-scale mining comprises an important source of supply to global supply chains. It is estimated that as much as 15% of cobalt mined in the DRC originates from artisanal mine sites.
Recognising its developmental potential as a livelihood source, artisanal mining has been recognised alongside industrial mining in the DRC’s mining code – regulation of the artisanal mining sector, however, is yet to be fully enforced.
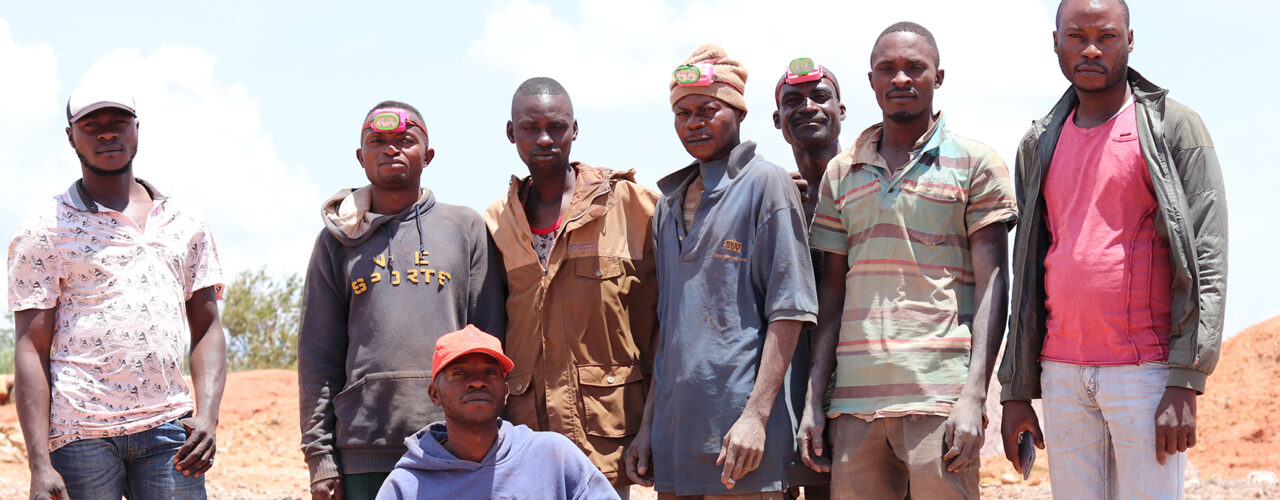
Pit owners and diggers
ASM sites comprise many — sometimes thousands — of vertical excavations or pits that burrow tens of metres to access cobalt ore. Pits are controlled by individual pit owners either by virtue of ownership rights to the surface land areas from before the mine site opened (as is the case for many of the pits at Kasulu) or because the cooperative at the site has determined the allocation through a process that appears to be reasonably transparent and widely understood. The pit owner’s participation in the workings of the pit ranges from an arm’s length relationship extracting a fee or rent from the digging team, to being quite involved and providing working capital for a pit team to pay for food and to buy basic equipment and even managing the organisation of the operation itself.
The pit is excavated by a team of 5–7 diggers (locally known as creuseurs) that either work inside the pit, carry bags of ore up the shafts to the surface, guard already produced ore, or coordinate the teamwork. These teams generally operate under a profit-sharing agreement with the pit owner. Usually diggers are provided with a small daily compensation for their time, which might be paid in cash or through the provision of food. The cooperative has the responsibility to ensure that agreements between pit owners and diggers are reasonable and fair. The frequency with which the cooperative mediates agreements is generally considered to be low, however.
Once sufficient ore has been aggregated at the surface of the pit, the pit owner, or a designated team member, transports the ore to either a trading station inside the ZEA or to independent open trading zones where many traders are assembled alongside arterial roads. Where the pit owners participate significantly in working the pit, they can claim 50–60% of the earnings. Where they are not involved, the pit owner might typically expect 10% of the sales value. The remaining 40–50% of the revenue is divided between the team members after expenses — such as food, cash advances, and equipment — have been deducted. The split of revenue is evenly distributed among the digger team, except for the team leader or pit foreman who receives a higher share. The unit of sales, and thus also of revenue split, is the bag or ‘lot’ of cobalt ore.
According to a limited survey that was circulated to about 20 miners by the research team, and interviews carried out with cooperative leadership, the average monthly income for an ASM cobalt digger is between USD 160 and USD 190. When the price of cobalt was higher, diggers reported earning up to USD 450 every two weeks, and sometimes up to USD 1,000 a month. Without a more intensive study it is difficult to validate these figures, but it is important to note that the change in income for diggers in the months around the time of the research was conducted for this report was sudden and the subsequent drop in income negatively affected the mood of workers at the ASM sites.
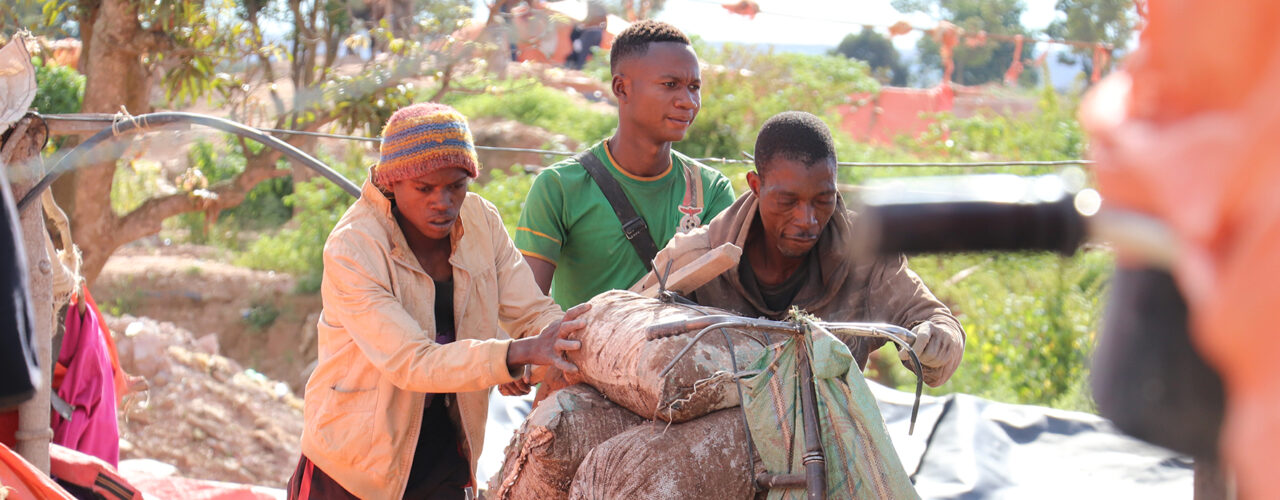
Transport
Once bags of ore are lifted from the pits, workers use bicycles or small trucks to transport ore from the pit to stations and depots where the cobalt is traded. These transport workers often work in pairs or groups of three to push and handle their bikes, maneuvering the heavily loaded vehicles through often-difficult terrain. Transporters are usually paid per bag of ore transported to its destination. The wage they receive depends on the distance travelled between pit and trading station.
From interviews with transporters and cooperative management, the research team found that for each 25kg bag, the team of transporters collects between USD 0.20 to USD 0.25. They can carry up to 20 bags per person each day, receiving a daily income of about USD 3.50 to USD 5.00, or approximately USD 70 to USD 100 a month. Of course, much depends on the availability of work and on the level of fitness enabling the transports to carry out their physically exacting activity.
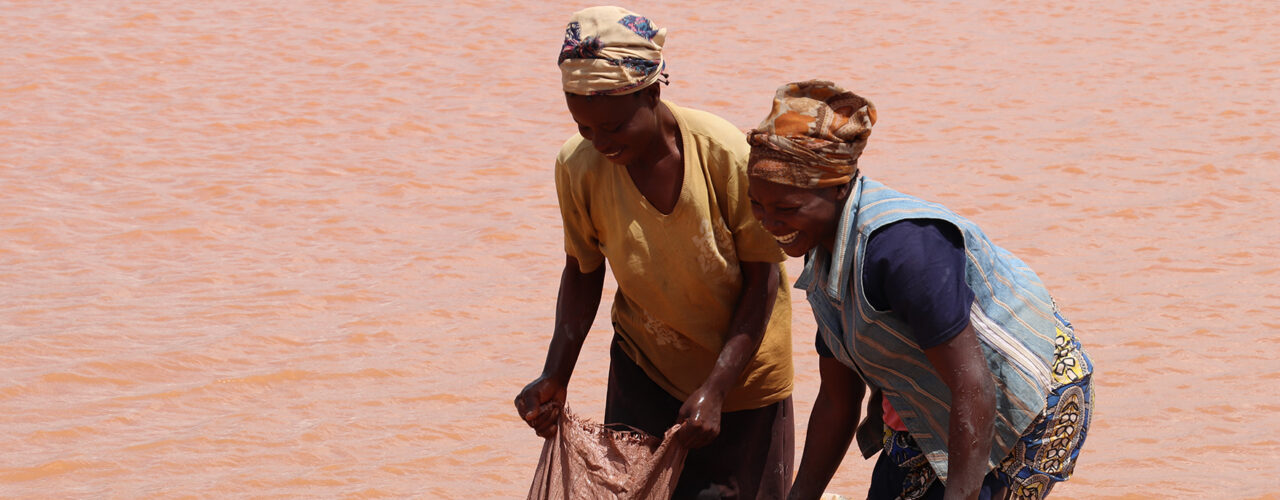
Washer
The task of washing is predominantly executed by women (locally known as lavages) receiving payment per bag of ore washed. Washing ore is one further step before hand-sorting ore for sale; washers are able to clean and identify rocks that contain the most ore and their purity through visual judgement, and thus increase the cobalt grade for each bag. The price–purity relationship increases rapidly before plateauing. The incentive is to do all that is economically possible to get the highest grade per bag through hand selection.
The washers usually stand directly in washing ponds using neither gloves or boots. Washers rinse off any dirt, by repeatedly lifting a metal net or a plastic bag lightly filled with ore using their bare feet. Washers operating in standing water, where the water is not changed regularly, and workers commonly report skin rashes and infections caused by exposure to the increasingly dirty water, presumably high in its concentration of heavy metals. When washers have the chance to wash in rivers or have the water replaced regularly, they usually do not encounter this issue, or at least not so severely.
In addition to their ‘per-bag’ payment, washers usually supplement their income by collecting ‘waste rock’ or ‘fines’ that are lost during the washing process, selling these collections of often low-purity material in bags at the trading station.
From interviews with washers and cooperative management, the research team learned that a washer receives about USD 2.50 for each bag, and that two bags is an average number washed per day. A very rough estimate of a washer’s income, therefore, is USD 5 a day, and the potential for approximately USD 100 a month.
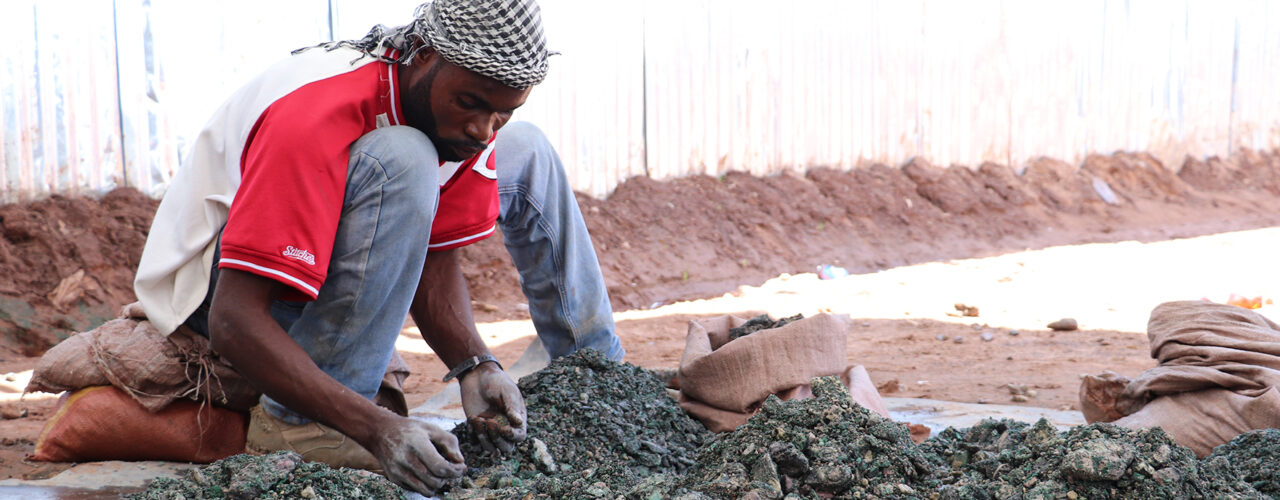
Sorting
Especially when cobalt prices are low, pit owners are incentivised to have their ore washed and sorted, or just sorted if there is not a lot of surplus mud or dirt in the bags. Sorting equally increases the total cobalt grade of the bag, achieving maximum economic return by separating and selling low grade and high grade separately. Such disaggregation can increase overall value. Both cobalt (black) and copper (green) can be identified by a trained eye.
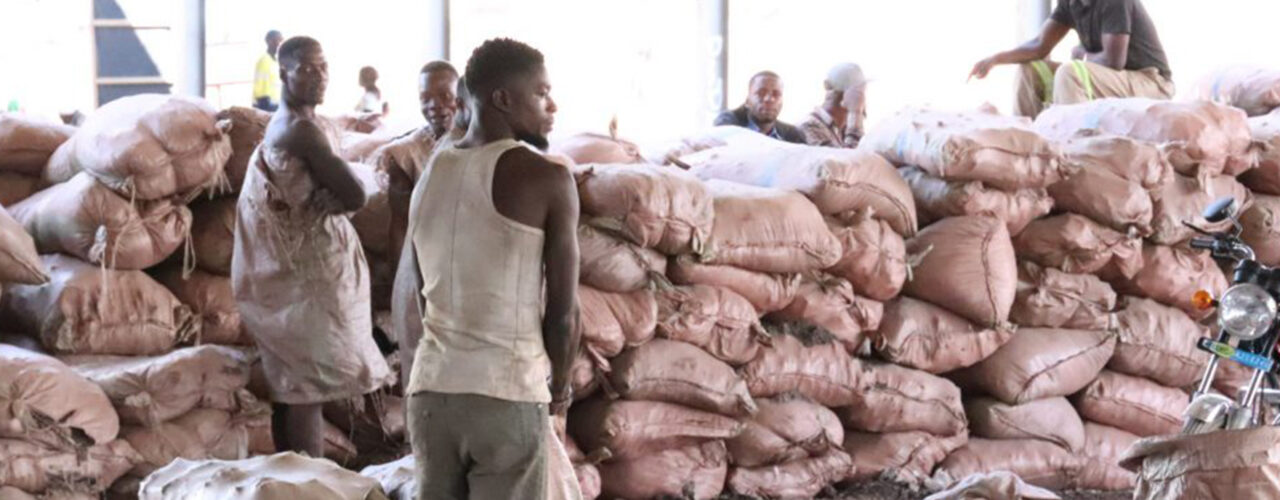
Trader
Selling and buying of cobalt happens between traders, locally referred to as Négociants, at depots buying large amounts of cobalt before selling them on to crude refineries. The role of being a Négociants is a designated role overeen by cooperatives.
Once washed and sorted, Négociants aggregate and sell cobalt ore either to one of the several depots located on site (in the case of various ASM projects) or to an ‘open market’ outside the ASM site, such as the Musompo or Kapata markets. Traders can be members of pit teams, or independent middlemen offering pit owners and diggers immediate cash, often without measuring the purity of the bags. Diggers can also choose to sell their ore directly to the on-site depots, but since sampling and selling can take quite some time, higher volumes are needed to sell directly.
Depots, often fronted by Chinese or Lebanese staff, take a sample of the bags that are for sale, assessing batch purity most commonly using an XRF machine, locally referred to as Metorex (a brand name of a particular product). To be accurate, these machines need to be carefully calibrated; there is currently no structured system to easily verify accurate calibration. Many diggers and even SAEMAPE personnel, voiced their concerns regarding the purity and weight assessments made by depots, claiming they were not accurate and implied that the traders were not being transparent about how the measurements are determined.
Once the purity is determined the bags are weighed on industrial scales and the sellers are paid either in cash or using MPESA, a local mobile money-transfer solution. Prices are often identical from one trader to the next. The depots at Kasulu only pay for the cobalt content of the ore, while the depots at Kamilombe pay for both copper and cobalt. Some depots run reward programmes offering premiums for large volumes of ore, which might include bags of baking flour, cell phones or even motorcycles. The depots sell their ore directly to crude-refiners, who organise truck transport from the mine to their facilities.
It was not possible to gain an understanding of the traders’ profit margins within the scope of this research, although the price paid for cobalt ore at depots is further discussed in section 1.4. Various interviewees explained that depots have been known to provide loans to pit owners and diggers in need of capital to improve their productive capacity by purchasing machines to pump air into deep pits, jackhammers and winches. These loans are repaid through a discount against the ‘lots’ sold at the depot. It is not possible to determine the frequency of these loans, but interviewees said that such loans were ‘quite common’.
Current mining conditions are unacceptable
Over the last years, issues around hazardous working conditions and trade terms perceived as exploitative have increasingly been put in the spotlight. Experts agree that most artisanal cobalt mining sites in the DRC lack adequate equipment, technical expertise and management systems to ensure the physical health and safety and mental well-being of mine workers.
Men descend down makeshift tunnels, reaching depths of up to 100 meters, despite the legal maximum depth being limited to just 30 meters. Without adequate PPE, too often, these conditions result in injury or even death that could have been prevented through better site management and enhanced infrastructure. Even the women in the washing and sorting stations face serious health risks due to high exposure to heavy metals. However, only the best run sites have access to emergency equipment and clinics.
On top of these occupational health and safety concerns, ASM sites see several other labour related issues. Artisanal mines often operate illegally or at least informally, lacking the appropriate licenses and land rights to conduct their operations. Miners often feel exploited by traders; and child labour inside the mines has been described as a systemic issue by research published by Amnesty International and Berkley University as early as 2016.
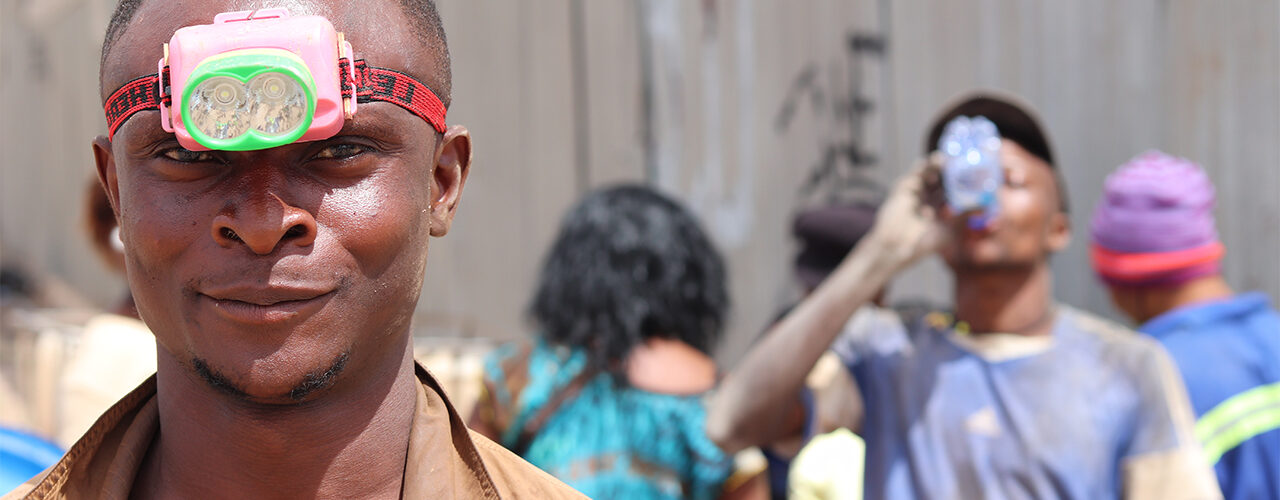
Mining can be done right
Improving ASM working conditions starts with engagement and investment into safer, dignified working conditions
Shutting down ASM altogether would be economically devastating and counterproductive. Rather than disengaging and turning a blind eye to these issues, we want to invest in, and engage with these sites promoting and enabling continuous improvement. We need to invest in on-site improvements regarding production equipment, mine infrastructure, and worker training. Over time, it is essential that artisanal, non-mechanized mining is transformed into small-scale mining with appropriate safety measures, earth-moving equipment, legal status, and pricing transparency so that miners are afforded safe and dignified working conditions.
Mine Diagram
Our vision for a modern mine site. Improving ASM working conditions starts with engagement and investment into safer, dignified working conditions.
Wall / trench – Ingress Control
The easiest and most efficient ways to keep children and unauthorised individuals out of mines is by securing the perimeter using a form of border protection.
Warehousing / depot following open market principle
Having various depots / buying centres on site leads to a controlled open market environment, where depots compete with one another for supply, giving miners a greater choice of where and at what price to sell their produce compared with the centralised buying model of some ASM sites.
Independent provision of productive equipment
In an effort to boost occupational health and safety on site as well as the level of productivity, and thus miners’ income, it is of high importance to make safe and good equipment available to the miners. Equipment could be anything from adequate head torches integrated in hard hats, through jack hammers and water pumps, to winches or essential PPE.
Independent scales and purity measurement to guarantee fair markets
Rampant mistrust in depots’ scales and purity measurements warrant the provision of independent verification booths that could be operated either by the cooperatives or potentially SAEMAPE.
Sanitation Facilities
Providing showers and toilets on site is an important step towards offering dignified and good working conditions.
First Aid Clinic
Minor accidents and injuries are a daily reality on the ground. Providing adequate first aid facilities, including trained staff is of great importance.
Fresh water access
Rather than being available at just one spot on the perimeter, workers should have access to free, safe drinking water.
Food Stores / Vendors
Easily overseen, local vendors play a big role in keeping the mines running, as they provide food, tools and even clothes to everyone working in and around the mine.
Weighing bridge
Before shipping the ore off to the refinery, trucks need to be weighed to calculate transport taxes.
Planned mine area and controlled pits
The core piece of the model mine is a controlled and planned mining area, governed by the cooperative in charge and monitored by SAEMAPE and other service providers. Congolese law restricts maximum pit depth to 25m, meaning that regular levelling, applying an open pit approach to the mine, allows full respect of the law.
Earth moving equipment
Excavators and other earth moving equipment should be on site to level sections of the mine area, where pit depth has reached or exceeded the legal maximum value of 25m.
Mine Security
Ensuring the peaceful operation of the mine and preventing unauthorised people from entering the mine requires the presence of mine security, usually comprising state mine police and private security, who should be trained with respect to the Voluntary Principles on Security and Human Rights.
Controlled Mine Access
Controlling access to the mines through gate controls ensures that intoxicated people, children and heavily pregnant women cannot easily enter the mine. Ideally, mines would devise a system of using personal ID cards for identification of workers authorised to enter the premises.
Traceability / Chain of Custody
To ensure the integrity of the ESG claims made around the minerals produced, it is important to utilise a credible chain of custody solution in line with international expectations for traceability.
The easiest and most efficient ways to keep children and unauthorised individuals out of mines is by securing the perimeter using a form of border protection.
Having various depots / buying centres on site leads to a controlled open market environment, where depots compete with one another for supply, giving miners a greater choice of where and at what price to sell their produce compared with the centralised buying model of some ASM sites.
In an effort to boost occupational health and safety on site as well as the level of productivity, and thus miners’ income, it is of high importance to make safe and good equipment available to the miners. Equipment could be anything from adequate head torches integrated in hard hats, through jack hammers and water pumps, to winches or essential PPE.
Rampant mistrust in depots’ scales and purity measurements warrant the provision of independent verification booths that could be operated either by the cooperatives or potentially SAEMAPE.
Providing showers and toilets on site is an important step towards offering dignified and good working conditions.
Minor accidents and injuries are a daily reality on the ground. Providing adequate first aid facilities, including trained staff is of great importance.
Rather than being available at just one spot on the perimeter, workers should have access to free, safe drinking water.
Easily overseen, local vendors play a big role in keeping the mines running, as they provide food, tools and even clothes to everyone working in and around the mine.
Before shipping the ore off to the refinery, trucks need to be weighed to calculate transport taxes.
The core piece of the model mine is a controlled and planned mining area, governed by the cooperative in charge and monitored by SAEMAPE and other service providers. Congolese law restricts maximum pit depth to 25m, meaning that regular levelling, applying an open pit approach to the mine, allows full respect of the law.
Excavators and other earth moving equipment should be on site to level sections of the mine area, where pit depth has reached or exceeded the legal maximum value of 25m.
Ensuring the peaceful operation of the mine and preventing unauthorised people from entering the mine requires the presence of mine security, usually comprising state mine police and private security, who should be trained with respect to the Voluntary Principles on Security and Human Rights.
Controlling access to the mines through gate controls ensures that intoxicated people, children and heavily pregnant women cannot easily enter the mine. Ideally, mines would devise a system of using personal ID cards for identification of workers authorised to enter the premises.
To ensure the integrity of the ESG claims made around the minerals produced, it is important to utilise a credible chain of custody solution in line with international expectations for traceability.
Transforming the sector through a continuous improvement approach – built on the notion of inclusivity.
In order to achieve better working conditions across the sector, we need to invest through blended finances, leveraging commercial offtake as well as grants from corporations, institutional donors and governments.
The FCA offers a platform for all parties to pool their funds together to work following an ambitious, yet pragmatic, continuous improvement plan, promoting inclusive development to ensure sustainable livelihoods for those working at mine sites.
Developing a framework for the engagement with and investment in responsible ASM Cobalt
In collaboration with the Responsible Cobalt Initiative (RCI) and the Responsible Minerals Initiate (RMI), the FCA has developed a holistic Environmental, Social, and Governance (ESG) framework, called the ASM Cobalt Normative Framework to establish best practices for structuring engagement and investment. This framework was developed in consultation of cooperatives, local and national government, downstream and midstream companies to ensure the inclusivity of all relevant stakeholders.